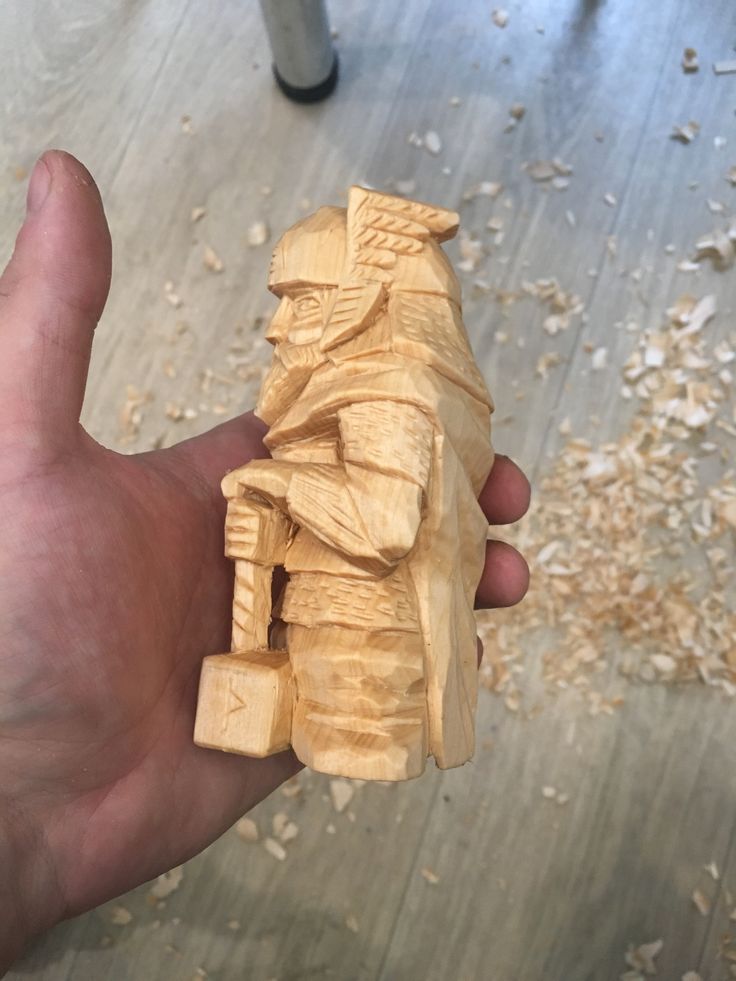
There are several things you should keep in mind when looking for an oar-carving knife. Size, sharpness, stag bone, lamination, and origins are all things to consider when you're purchasing your knife. This article will help you choose the best knife for your needs. After reading this article, you'll have an idea of what to look for when purchasing your new oar carving knife.
Size
Oar Carver pocket knives are the best examples of this art. There are currently three sizes to choose from in the current lineup. Version 2 is larger and has a thinner blade, while Version 3 is slightly larger with a thicker blade and a wider gap between the two. Here are some tips to help choose the right size.
Sharpness
A sharp edge is an important aspect of any oar carving knife. You should keep your knife's edge sharp. Your knife will begin to show signs of wear like chips, dullness and nicks. Luckily, it is relatively easy to gauge the sharpness of an oar carving knife by observing the edge. A magic marker can be used to match the angle between the blade's centre and the knife's edges.
You can test the sharpness by cutting a piece from basswood across its ends grain to determine if it is. A blade should be perfectly sharp when it cuts through the wood without leaving ripples or drag marks. A smooth cut is similar to cutting a baby's bottom with no marks. If the blade leaves any of these marks, the blade may not be sharp enough for carving. It is vital to ensure that the sharpness, or oar carving knives, are checked regularly.
Laminated blades
The Oar Carver series was designed by Ross Oar, a world-renowned carver, and has been a timeless example of the carving pocket knives. Currently, there are three models, Versions 1, 2 and 3. Each version is remarkably different from the previous one. Version 2 has a wider gap between the blades. It also has a shorter edge. You can find more information in the Oar Carver blade guide.
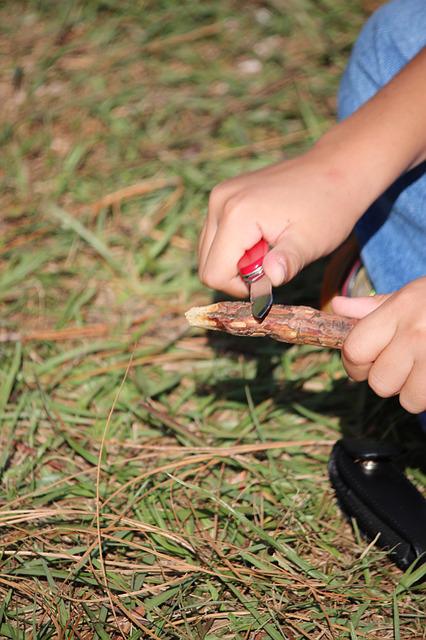
Mora makes the 106, and 120 versions. Both models are made with a laminated steel blade, but the Mora knife is longer. Both knives have a basic oval handle, and are also sold with a snap sheath. The Mora Frost 122 is another model that features a laminated carbon and steel blade with a 61 Rockwell-hardness. This knife is perfect for carving. The blade is also sharp and long-lasting.
Origins
The oar carving knife was developed from ancient times in Japan. It is made of solid wood and has a narrow circumference. The handle measures approximately four and a third inches. The oar has an oar with a long, flat blade and a flat top. The blade of the knife measures 53 inches. The handle is carved into a narrow circle, while the blade and shaft are separated by a thin section of wood.
The earliest known carving tool is the oar, but its history runs much deeper. The oar originated as a tool for riverine and coastal populations. Because the Admiralty recognized the symbol easily and it was widely used, they chose the oar. Although the oar may have had different meanings, they are still useful. Below are some of its possible origins. If you are interested in learning more about the history and evolution of knife-making, they are also worth looking at.
FAQ
How often do I need to buy new supplies
Some tools will need to be replaced over time. You'll need to sharpen your hand tools regularly if you use them. You'll also need to replace parts if you use power tools. Spread your purchases over several months to avoid purchasing too many items at once.
How can I learn basic woodworking skills
You can start building furniture by making a bench. This project can be done with any kind of wood that you have at home. If you don't know what kind of wood to use, then go ahead and buy some cheap pine boards from Home Depot or Lowes. After you've constructed your bench you'll want sand all the rough edges off and varnish it.
How do I identify the type of wood that I am dealing with?
When purchasing wood, always check the label. The label should include information about the wood species and its moisture content as well as whether or not it has been treated using preservatives.
What is the difference between a hobbyist or a professional woodworker, and how can you tell?
Hobbyists enjoy making things out of wood, whereas professionals focus more on the quality of their work. Hobbyists usually take pride in their creations and often share them with friends and family. Before they start working on a project, professionals will spend hours researching the designs. They will meticulously plan every detail of their work from choosing the right materials to finishing it.
How much should a Woodworker Charge per Hour?
The hourly rate for a professional woodworker varies depending on many factors, including skill level, experience, availability, location, and other variables.
An hourly wage for skilled woodworkers is between $20 and $50.
A less skilled woodworker might charge as low as $10 per hour.
What is the difference between plywood and particle board?
Plywood is made up of layers of wood pressed together under pressure. Plywood comes with a range of thicknesses, and it is most commonly used for flooring and cabinets. Particle board is made up of sawdust mixed in resin, then compressed into large pieces. This board is commonly used in home improvement projects. Both types of boards can be easily cut and are durable.
Statistics
- Overall employment of woodworkers is projected to grow 8 percent from 2020 to 2030, about as fast as the average for all occupations. (bls.gov)
- The best-paid 10 percent make $76,000, while the lowest-paid 10 percent make $34,000. (zippia.com)
- In 2014, there were just over 237,000 jobs for all woodworkers, with other wood product manufacturing employing 23 percent; wood kitchen cabinets and countertop manufacturing employing 21 percent. (theartcareerproject.com)
- If your lumber isn't as dry as you would like when you purchase it (over 22% in Glen Huey's opinion…probably over 10-15% in my opinion), then it's a good idea to let it acclimate to your workshop for a couple of weeks. (woodandshop.com)
External Links
How To
How to stain wood
The process of staining wood involves the application of chemicals to the wood's surface, which causes it to change its color. This chemical reaction changes the wood's color from white to brownish. Oak is the most commonly used wood for staining, but other woods can also be stained.
You can apply wood stains in many different ways. Mixing the stain in a solvent such as turpentine and spraying it onto the wood is one method. Others use a solution made up of water and dye, which is then applied directly onto the wood. You can mix stains into varnishes or paints to make them part of your finish coat.
Preparing the wood surface is the first step to staining it. The wood must be thoroughly cleaned to remove all grease and dirt. Sanding the wood smooths out rough spots and scratches. The next step is to choose the stain type you want. There are two main types of stain: non-penetrating and penetrating. Penetrating stains penetrate deeper into the wood than non-penetrating ones, making them ideal for dark colors such as mahogany. Non-penetrating oils work best when used with light colors, like maple.
Once you have decided on the stain type that you want, get your tools ready. You can use a paintbrush to apply stains. This allows you spread the liquid evenly over the surface. To remove any stains left behind after painting, you will need some rags. If you are planning to mix your stain, ensure you have enough containers for each component.
After you have prepared the materials, you can clean the area where you want to stain the wood. Use soap and warm water to remove dust and grime. Use a dampened sponge and warm water to clean the entire piece. Be sure to get rid of all loose material, especially if staining is planned for darker wood.
The stain should be applied next. Apply the stain by brushing or spraying it onto one side of the furniture. Work slowly and carefully, moving back and forth along the grain of the wood until you reach the opposite end. Keep the stain from dripping off the wood's surface. Before moving on to the next steps, allow the stain drying completely.
To protect the painted surface, apply a coat of clear polyurethane sealant. Apply three coats polyurethane sealer. Allow the third coat to dry overnight before sanding the final coat.