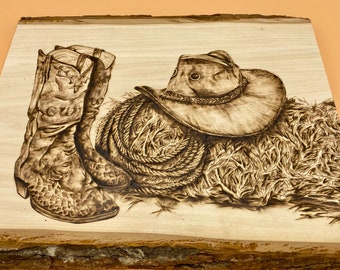
There are many materials that you can use for wood burning art. If you desire a clear color and no grains, basswood may be the best choice. This wood is expensive and can be difficult to find in the right size. Birch wood, another popular material, has a fine texture with a bright color and no differences in the annual growth rings.
Preparing the wood for pyrography
Preparing the wood for pyrography is the first step. Dark wood doesn't show the art well, and a prominent grain pattern makes it difficult to work. Also, pyrography is not a good choice for uneven or resinous timber. Use natural wood that has been sanded and treated with no chemicals. Once you have prepared the wood, you are ready to start burning!
Shellac is an option to seal pyrography project, but this is only temporary. Shellac is a heat-resistant compound that discolors wood and should be avoided on cutting boards and coasters. A cheaper alternative to shellac is paste wax. Paste wax gives wood a smooth, natural sheen when it is applied. It is easy to apply, and it looks natural.
Wooden design:
Start by drawing a sketch of the design you wish to incorporate into your wood burning art. You can use a pencil, eraser or ruler to create the design. Premade stencils are particularly useful. Wood burning sets for beginners can be purchased that include all necessary tools. These are some woodburning design tips to get you going.
The art can also be painted. You can use a pointed pen or a flat one. It is important to not burn too deeply, or your work will be damaged. Your wood burning art can be painted or shaded. After you are done, you can add color to your wood burning art. After the wood has cooled down, you can add shading.
Creating Lichtenberg burns
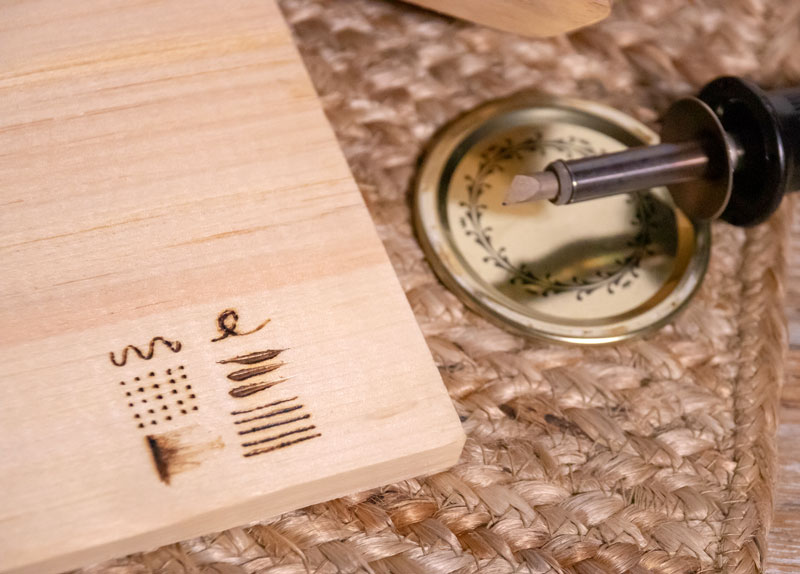
The art of creating Lichtenberg burns has a lot potential. Using a microwave transformer and a high voltage, you can create branching electrical discharges. Lichtenberg first discovered Lichtenberg figures in 1777. Lichtenberg's wood burning is becoming a more popular form of art thanks to fractal wood burning. These figures can be created using the following steps:
Before you begin, you'll need some safety equipment. You will often use high-voltage Transformers to power appliances and neon signs. These transformers have a higher chance of electrocution due to their vulnerability to live wires and unprotected. Also, you should wear gloves when operating a Lichtenberg device. You should also wear rubber gloves. You should use gloves to protect your hands. Even though you might be electrocuted even if your hand touches an energized electrode for a while, it won’t cause your heart to stop beating. Another thing to remember when using a Lichtenberg device is to bring someone with you to help you. You can rely on this person to help turn off the electric current if you need it.
First, you need a power source. A high-voltage, electrical source is required to power a Lichtenberg device. In order to burn wood safely, the electric current used must not exceed 2,000 V. The majority of woodworking associations forbid the use this technique. Safety is the number one priority, no matter what your intention is to create a Lichtenberg shape. When working with electricity, always wear gloves and protective clothing. Also, double-check your electrical outlet before you make contact.
Use a stencil
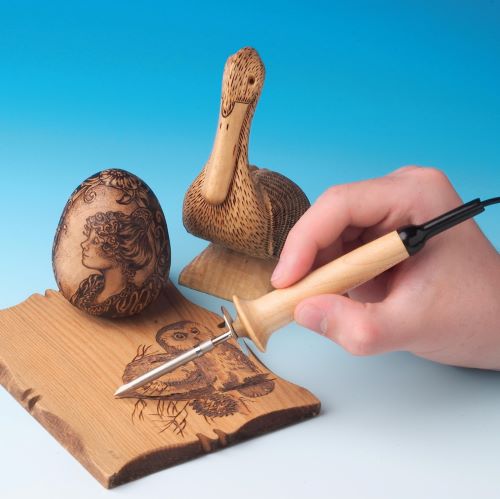
If you are looking to create intricate wood-burning designs, a stencil is an ideal tool. A stencil can be used to trace a design onto graphite sheets and then transfer it to the wood. You can use the stencil as a guide to your hands and eyes. However, the final design is up to you. While it is possible to use a pencil to draw a pattern, holding the stencil and the wood at the same time can result in burns.
First, you need to sand the wood on which you'll be burning the image. Once the wood is smoothed, it's time to start designing. To ensure that your design is as clear and precise as possible, apply some pressure to transfer the graphite into the wood. When you're done, you'll have to remove the tracing paper.
FAQ
How do I learn basic woodworking skills?
Building a bench is a great way to get started in furniture building. This project can easily be done using whatever wood you have at your house. If you're not sure which kind of wood to choose, you can purchase cheap pine boards at Lowes and Home Depot. After you've built your bench, you'll want to sand off all the rough edges and finish it with a stain or varnish.
Does it take a genius to make woodworking work?
No. Woodworking is not rocket science. Anyone can learn to use basic powertools and techniques to create beautiful work of art.
What is the minimum investment a hobbyist needs to make in order to get started?
A lot of capital is required to purchase the necessary supplies and tools if you want to start your own woodworking shop. A good place to start would be by buying a small table saw, drill press, circular saw, jigsaw, and sanding machine. These items aren’t too expensive so you won’t have to break the bank.
How often should new supplies be purchased?
Over time, you may need to replace your tools. If you are using hand tools, you will need to sharpen them frequently. For power tools, replacement parts will be required frequently. Avoid buying too many products at once. Spread your purchases out over several months.
What type of wood should I choose?
Woodworking is a popular job that involves oak, pine and maple. Each type of wood has its own unique characteristics that can affect the final product's appearance. Oak, for instance, is darker and harder than most other woods. Birch is lightweight and soft while mahogany is heavier and denser. You also have the option of solid wood or veneers. Veneers consist of thin sheets made from wood and glued together to form a single layer.
Where can I start woodworking?
You can learn the most effective way to build furniture by actually building it. You will need tools. There are bound to be mistakes. But if your persistence is consistent, you will soon master the craft.
First, choose a project you would like to complete. You could make something as simple or complex as a box. Or you could build a whole entertainment center. Once you have settled on a specific project, it is time to find a woodworker in your area who is experienced in such work. Ask them for suggestions on the tools you will need and where to buy them. Maybe you can ask the person if they know of anyone who does this sort of work.
Which woods are good to use for furniture-making?
Woods are classified by their hardness. Softwoods are pine, cedar and cypress. Because they are resistant to rot, softwoods are often used as outdoor furniture. These hardwoods include maple, mahogany and teak. Because they are not weather-resistant, they are best used indoors.
Statistics
- In 2014, there were just over 237,000 jobs for all woodworkers, with other wood product manufacturing employing 23 percent; wood kitchen cabinets and countertop manufacturing employing 21 percent. (theartcareerproject.com)
- Most woodworkers agree that lumber moisture needs to be under 10% for building furniture. (woodandshop.com)
- The U.S. Bureau of Labor Statistics (BLS) estimates that the number of jobs for woodworkers will decline by 4% between 2019 and 2029. (indeed.com)
- Overall employment of woodworkers is projected to grow 8 percent from 2020 to 2030, about as fast as the average for all occupations. (bls.gov)
External Links
How To
How to make wood joints
This tutorial will show how to join 2 pieces of wood together. We will be using the "pocket-hole joint", which involves drilling holes in wood and then gluing them together. This works well if the wood is straight and smooth. You might consider dowel joinery if your wood isn’t straight or flat. Here are the steps
-
Drill Pocket Hole Joints. Start by measuring and marking the spot where the pocket hole joint will be placed. Then drill 3/4 inch deep holes into the ends of each piece of wood using a jig saw or handheld drilling machine.
-
Sand Smooth. You can sand the edges of the wood to ensure that it doesn't split.
-
Glue Together. Apply glue to both ends of the wood. Allow the wood to rest for five minutes before clamping it together.
-
Connect the pieces. Once the glue has dried, clamp the pieces together so they are flush.
-
Trim Joinery. Trim any excess wood surrounding the joint once the glue has dried completely.
To be able to turn the pieces inside-out, leave enough room between them.